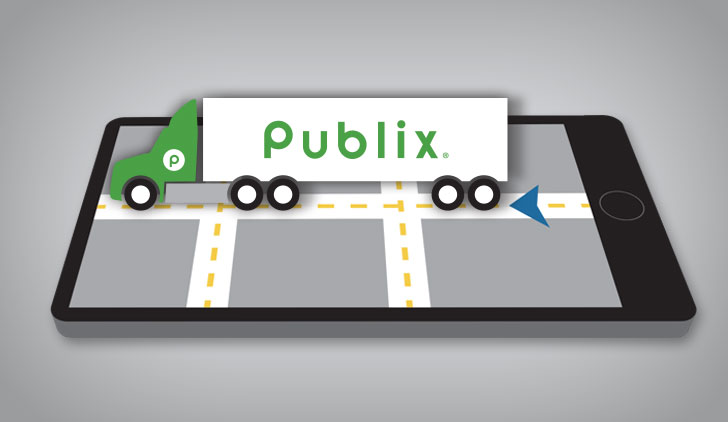
As soon as Hurricane Irma was forecasted to make landfall in Florida, associates in distribution began making preparations to provide stores and customers with the products they needed.
Distribution teams didn’t just prepare for the storm; they prepared for its aftermath as well. They began securing additional tractors, trailers and drivers, as well as scheduling outside carriers to assist in deliveries. By adding to their fleet and setting store order limits, the distribution team made sure they were ready for both the preparation and recovery efforts.
“We tried to increase the orders ahead of the storm, and thanks to our distribution associates who went above and beyond, we were able to serve our stores and deliver products as quickly and as efficiently as possible,” Vice President of Distribution Casey Suarez said.
In preparation for the storm, the fleet maintenance team removed equipment and potential projectiles like wooden pallets and crates from the docks and loaded the items from the return center into trailers to weigh them down against the wind. While some trailers were lined up along the exterior of the warehouses to protect doors from winds and flying debris, others were parked closely together — like a puzzle — to protect any tractors located in an open lot.
Rerouting
Although Irma caused many Florida warehouse and distribution locations to close, stores outside of the storm’s track were operating as usual, making it critical for some functions normally performed at the closed warehouses to be diverted to another distribution center.
“Our warehouse in Atlanta was able to reach the Florida Panhandle stores when the Jacksonville warehouse closed during the storm,” said Casey.
Destination ahead
Once the storm cleared and the winds slowed, the distribution emergency response team began the recovery process. Industrial maintenance teams surveyed the facilities for damage and found only a few fallen trees and broken signs. Materials from the docks were brought out of storage, and orders that had ceased during warehouse closures started trickling in.
“After the storm, order limits are increased slowly as the warehouse can select orders faster than drivers can deliver,” explained Casey. “We don’t want to create gridlock in the distribution centers. With this storm, our Orlando refrigerated facility was able to help us with deliveries, so we could complete orders at our other warehouses.”