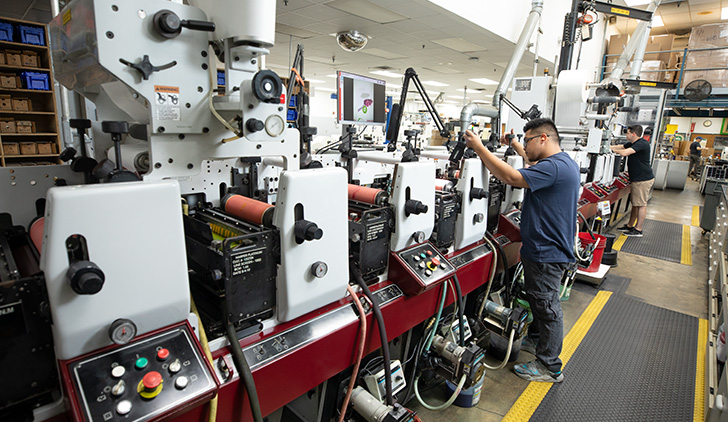
Our printing services facility in Lakeland, Florida, specializes in producing a wide variety of printed materials — everything from shelf tags to truck decals — sometimes even using 3D printers. Printed materials play an important role in our marketing and communication efforts to create a consistent brand image.
We have 4 main operations in printing
- label production
- item-level pricing
- large-format printing and
- mailing services.
Item-level pricing includes regular price tags, promo ad signs, menu boards over our deli counter, and the compare and save program you see in our stores. Large-format printing is all about those big signs that tell you where to find items like international products. Mailing services covers the direct mail you get at home to promote our products.
We’ll take a closer look at label production, our highest-volume operation. It includes creating labels for all products that we produce in our manufacturing facilities, such as milk, orange juice and deli items, as well as thermal and preprinted labels for items like subs, meat products and produce.
Step 1
Before labels are printed, the production team thoroughly assesses the business area’s needs. They begin by determining the equipment needed to produce the labels accurately. This includes considering the material type, the required shape and dimensions, the appropriate adhesive for the surface it will be used on and ensuring the label peels correctly. They also make sure barcodes are present and scannable on each item and that the rules and regulations for ingredients and allergens are followed.
Step 2
Once these tasks are complete and verified, a layout is created by marketing, and the labels are sent to a pre-press proofing team to check for accuracy. The team verifies the labels are correct and approved for print, and that the layouts match the templates. This technical job involves a bit of chemistry, since the team must understand how the ink will display on the printed materials and in stores (e.g., cold cases).
Step 3
After the artwork is approved, the next step in the printing process is making the printing plates. These plates are made of photopolymer — the same material used to make some ink stamps. Printing plates are created for every color visible on the label and mounted on one of our print presses. The print press used for labels is about 80 feet long and can print up to 17 inches wide with 8 colors.
Step 4
The paper is then checked to ensure it’s the correct one for the project and is then covered with a special glue, which will help the label stick to the products. The large rolls are fed into the press, where tension control is critical to prevent defects like wrinkling.
Step 5
Inks are applied using an anilox roller, which transfers a precise layer of ink onto the material. For quality control, operators measure and ensure color accuracy using specific tools. We then cover the labels with a protective layer to increase its life. Finally, the printed material is cut into the final label shape using a process that doesn’t cut the backing it’s on.
The finished labels are wound onto a large roll. The larger rolls are then run through a rewinder — a machine used to wind the material onto a smaller roll.
Once the labels are rewound, they are sent to our warehouses and/or manufacturing plants. If a store orders a label, it comes from the warehouse. Labels are applied to products at our manufacturing plants.
About printing services
Our manufacturing operations began in 1951 with our print shop. The printing services facility is more than 89,000 square feet and has 230 associates. Our only non-food plant, printing services operates 24 hours a day, 6 days a week to serve our stores and support locations. About 75 to 120 million labels are printed in an average month.